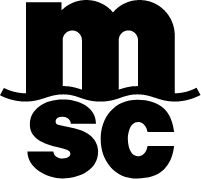
/de/lp/blog/industries/2023/automotive-supply-chain
Automotive supply chains: The key considerations
11/01/2024
In recent years vehicle manufacturers had to evolve their automotive supply chains in order to work with multiple suppliers to source all the different components required to construct each vehicle. This development has meant that the once simple supply chain has transformed into a ‘supply web’, with multiple threads all leading to the same end point.
Subsequently, the automotive industry has had to evolve in the way that they plan and consider their overall supply chain. Forward preparation means that businesses can maintain high levels of production and customers will continue to receive their goods on time. Because of this, more vehicle manufacturers are turning to shipping companies like MSC who have the experience, size and scale to enable them to offer businesses the necessary support throughout their supply chain.
It’s important to consider all the possible challenges that you may encounter throughout the supply chain to establish how best to overcome them. Planning solutions before problems arise can help prevent avoidable delays and help keep your overall supply chain moving smoothly.
Many automotive manufacturers also adopt a ‘just-in-time’ manufacturing process to match production with market demand. While this level of agility is hugely beneficial from a business and profitability perspective, it also makes it even more crucial to minimise possible supply chain issues to avoid product shortages and loss of revenue.
Other common challenges faced throughout the automotive supply chain include:
• The need for numerous spare parts which can be used throughout the manufacturing process.
• The production of different parts in various locations across the world.
• Stringent quality control processes for component parts and completed vehicles.
• Delays impacting transportation speed and reliability.
Fortunately, the developments made in the automotive industry in recent years mean that there are new technologies available to help manufacturers overcome certain challenges they face. For example, new tracking systems and the development of a supply chain management systems cloud ensures that businesses have a clear overview of where different components are within the overall supply chain. As a result, it becomes easier to optimise the different stages in your automotive supply chain more effectively as all decisions can be based on real-time data.
Equally, working with a shipping partner like MSC who has decades of experience in the automotive industry means you’ll be partnering with a company that have the foresight to offer the ideal solution to help you optimise your supply chain flow and offer you the flexibility to cover any fluctuation in demand. When you combine this human expertise with advanced technology, you’ll find yourself in a strong position to overcome or resolve any challenges that arise throughout your supply chain.
Electric Vehicle Supply Chains Need to be Thoroughly Planned
The vast expansion of the electric vehicle market has turned them into a key consideration for all vehicle manufacturers. As the required components of an electric vehicle involve more raw materials and production stages, there is an increased likelihood of encountering additional problems during production. As a result, your electric vehicle supply chain needs to be thoroughly planned before manufacturing can start.
Electric Vehicle Supply Chains Need to be Thoroughly Planned
The vast expansion of the electric vehicle market has turned them into a key consideration for all vehicle manufacturers. As the required components of an electric vehicle involve more raw materials and production stages, there is an increased likelihood of encountering additional problems during production. As a result, your electric vehicle supply chain needs to be thoroughly planned before manufacturing can start.
One of the key components of an electric vehicle is lithium-ion batteries, which rely on the export of raw materials from countries like China, Indonesia, and the Democratic Republic of Congo. Currently, most electric vehicles that contain lithium-ion batteries are manufactured in China, Japan, and South Korea. With so many different locations required for battery production, vehicle manufacturers need to think ahead for potential delays with both the sourcing of raw materials and the transportation of the completed batteries across the world.
Similarly, when it comes to the shipping stage of your automotive supply chain, vehicle manufacturers need to consider current regulations. As lithium-ion batteries are considered a dangerous good and need to be removed from the vehicles before they are shipped, this increases the amount of time needed once the electric vehicle has been unloaded from the vessel before it can be delivered to the customer to allow for the battery to be reconnected and the product tested.
To enhance your overall automotive supply chain, it’s important to consider and understand how the different tiers feed into one another. As a business, it’s also crucial to have visibility on which supplier is responsible for providing or producing each part. That way, you’ll be able to monitor the different locations of the various parts required for manufacturing, meaning you can anticipate and overcome any potential problems more quickly.
Automotive part suppliers are broken down into three tiers:
Tier one suppliers
Tier one suppliers provide completed parts and components to the manufacturers. Many vehicle manufacturers will have a direct relationship with specific tier one suppliers depending on the make or model of the vehicle they produce.
Tier two suppliers
Tier two suppliers also supply completed parts; however, these are not limited exclusively to the automotive industry . Tier two suppliers may also be producing parts that are required by tier one suppliers to make the finished products.
Tier three suppliers
Tier three suppliers are more removed from the finished product compared to tier one or two suppliers. They are responsible for ensuring that all the necessary raw materials are available for use by tier one and two suppliers.
The best way to overcome potential challenges that can occur within an automotive supply chain is to consider how best to optimise your overall business strategy.
For vehicle manufacturers, one way of doing this is through vertical integration. This enables individual businesses to control their overall supply chain and multiple stages of the production process. This affords better supply chain visibility and gives businesses increased control over production. With so many strings to the automotive ‘supply web’, having better clarity and control over each one enables manufacturers to be more agile in how they organise their supply chain and increases their ability to react quickly should problems arise.
Ask MSC
At MSC, we pride ourselves on using our decades of experience to help you optimise your supply chain effectively and be flexible as the market changes with consumer demand. Our global fleet, combined with extensive port coverage and land transportation solutions also means we have the scale to effectively help you adjust your supply chain and ensure that your overall manufacturing processes aren’t impacted. We offer a range of end-to-end transportation and logistics solutions, all of which can be tailored to the needs of our customers.
Contact us today to explore how MSC’s full range of shipping and transportation solutions could be beneficial for your business.